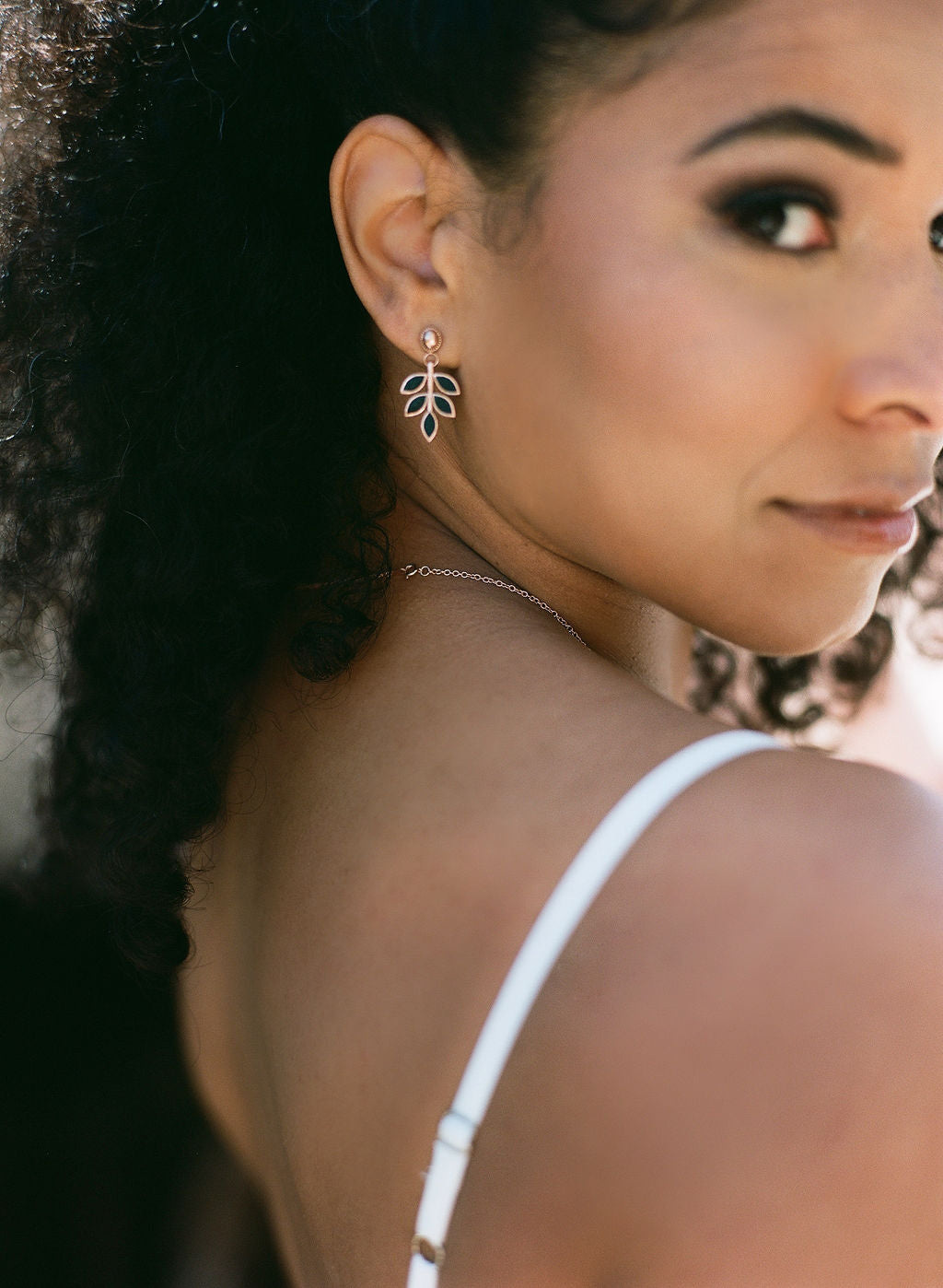
Our Promise
At Northwood Custom Jewelry, our promise is to warmly welcome you into a world of authentic craftsmanship and genuine connections. We believe in crafting jewelry that resonates with your individual story and values, blending timeless elegance with modern creativity. From restoring cherished heirlooms to designing personalized pieces, we're dedicated to infusing every creation with meaning and beauty. When you choose us, you're not just a customer – you become part of our journey, and we become part of yours. Your satisfaction is our commitment, and your journey with us is one that's treasured, unique, and unforgettable.
Embracing Our Values
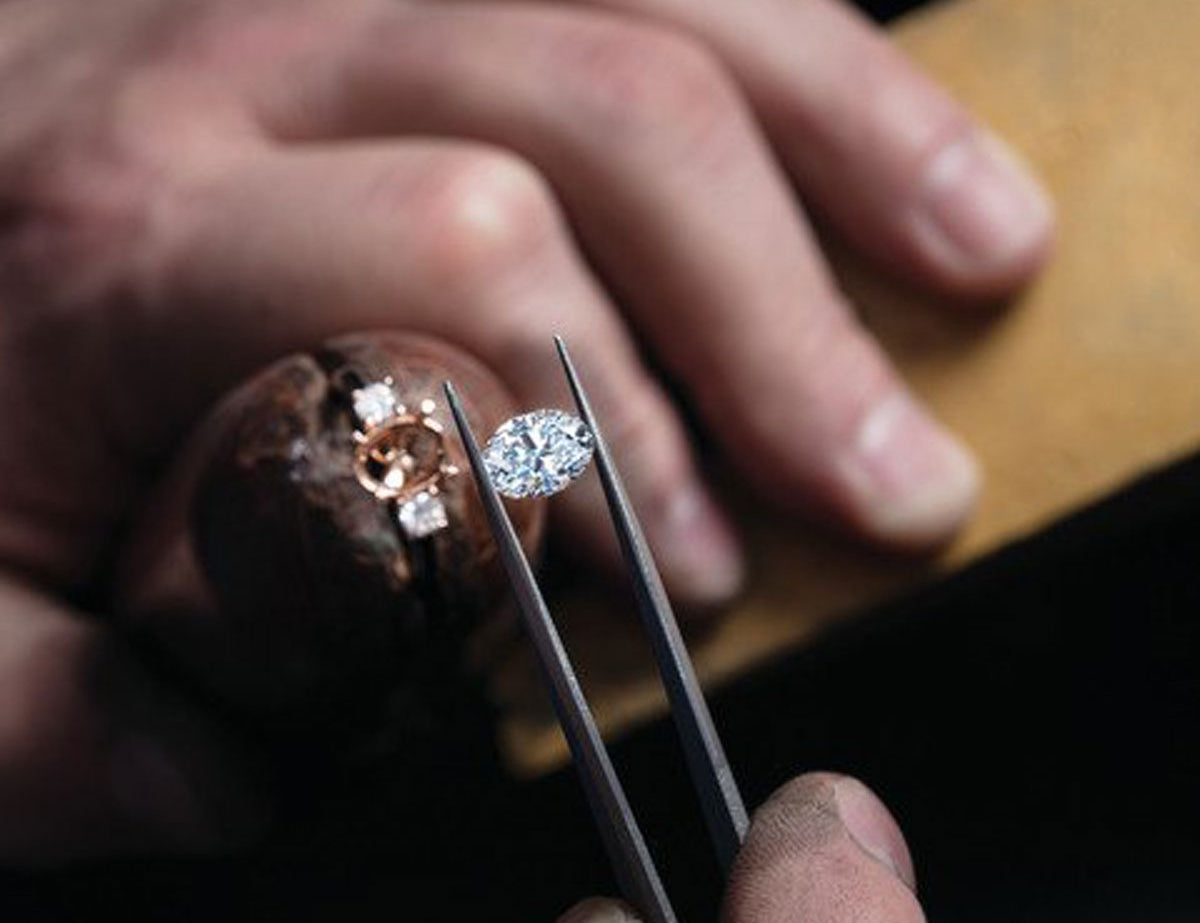
Craftsmanship
Rooted in ethical values, our expertly crafted pieces come to life with genuine care and attention to detail, ensuring enduring beauty for generations to come.
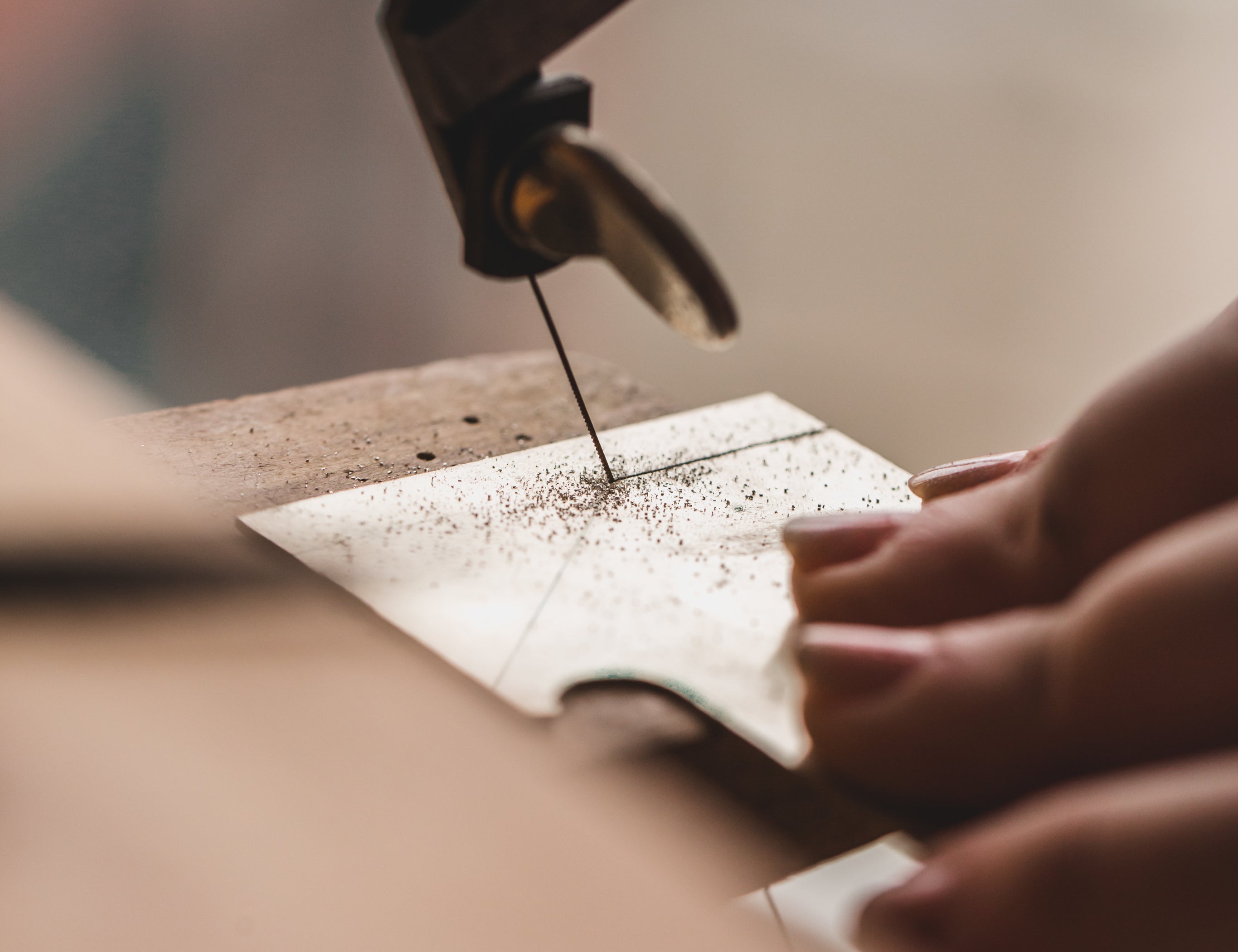
Creativity
Our designs are born from the fusion of your goals and desires and our insightful creativity, resulting in truly one-of-a-kind jewelry that celebrates your individuality.
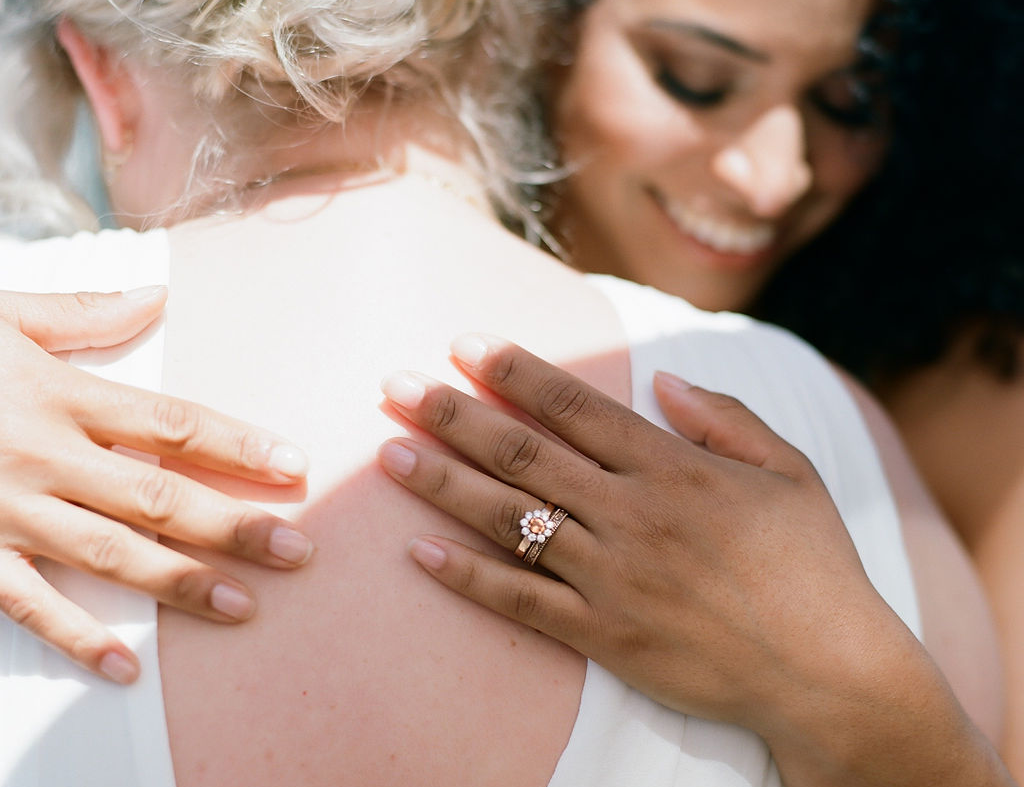
Connection
Beyond jewelry, we nurture heartfelt connections, forging meaningful relationships with our valued customers, and becoming a part of their cherished stories.
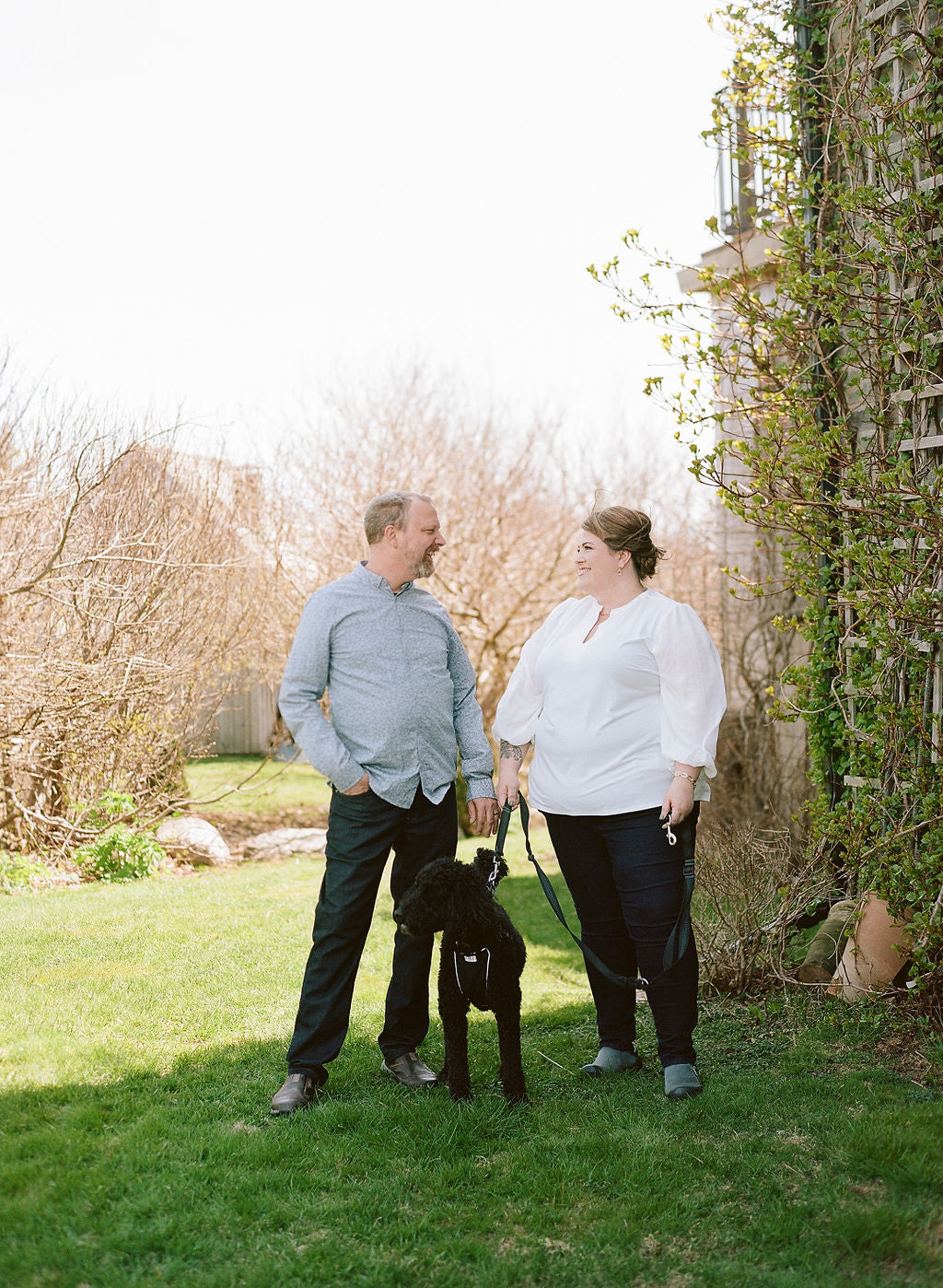
Meet the Hills
Best friends and co-founders, Allan and Laurel Hill, met while working in the same hotel. They were married two years later, and have worked side-by-side together ever since.
Northwood started as an Etsy store selling rings made entirely from wood in 2012, but quickly grew in popularity.
As the business grew, so did the interests of the Hills. Allan went to California to learn lost-wax-casting and started working in gold and precious metals, while Laurel took up Computer Aided Design and 3d Printing in order to bring more complex styles to Northwood.
Today they've opened a full-service Jewelry store in their local community and focus on custom design for customers around the globe and close to home.
Our Commitment to Inclusivity
Everyone is Welcome
Our jewelry celebrates the diverse tapestry of humanity – a canvas for all to express themselves, regardless of size, gender identity, or the form of love they hold dear.
At Northwood, inclusivity is our heartbeat, and every piece we craft is a reflection of this commitment to embracing and celebrating all.
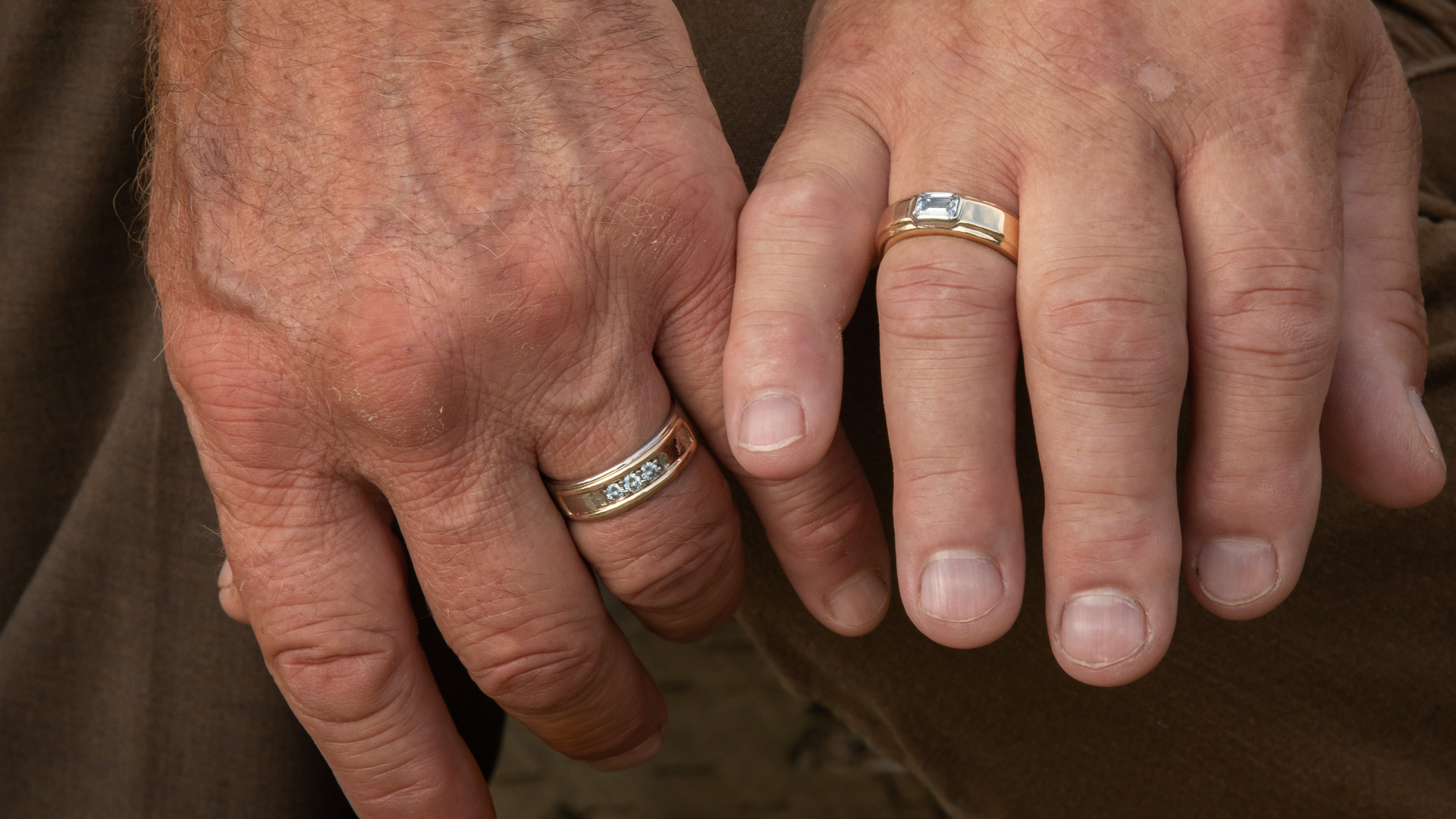